Comprehensive manufacturer guarantees help to promote a ‘systems approach’ to construction, by giving specifiers the confidence that the chosen combination of products comes from a reputable and traceable supply chain.
When we talk about traceability, we mean an understanding of where a product – or, in the case of a system, a collection of products – has come from. Traceability is therefore multi-faceted. Without it, how can specifiers know they’re choosing a solution that will perform as intended? And how can they know the system will also contribute to the project’s environmental impact goals?
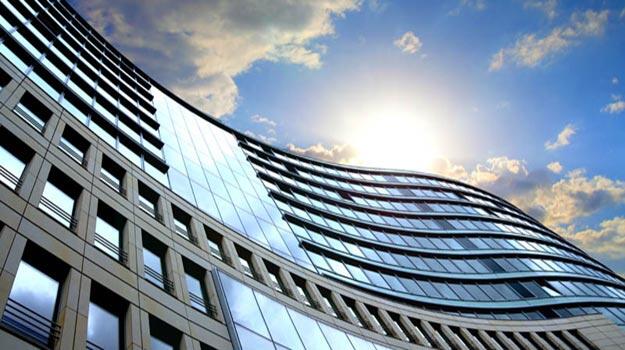
Why do specifiers want system guarantees?
It’s not unreasonable to suggest that, in trying to design for lower environmental impact as well as for building performance and occupant comfort, the job of the specifier has become more challenging.
Sourcing components from multiple manufacturers has always been a time-consuming effort, which doesn’t necessarily offer much certainty. Even if all manufacturers confirm the suitability of their product in a proposed design, there’s an ever-present risk that they’ll find a reason for their product not to be at fault should a design fail on site.
Now, specifiers also require detailed and accurate information about environmental impact, to help protect building users from the effects of changing climate, and to reduce the impact of human activities on natural habitats. Obtaining all of this information from multiple sources, and then interpreting it, is a mammoth task.
In this context, a system approach really comes to the fore. All of the components come from a specified supply chain, reducing the workload of the specifier, building resilience into the design of the built environment, and providing certainty in the form of a system guarantee.
Asking questions about traceability
Certainty about meeting the requirements of national building regulations, and gaining credits as part of voluntary standards, has always been an argument in favour of systems. When products come from a traceable and reputable supply chain, they can be relied upon to perform in accordance with test results and certification.
The question of product specification in a climate and biodiversity emergency, and the imperative to reduce environmental impact, is changing the questions that specifiers ask of manufacturers.
Simply saying that materials and products are ‘sustainable’ is not enough in itself. Sustainability has to be verifiable. That requires manufacturers to act responsibly - both in their own business, and in who they choose to deal with in their supply chains - and report on the impacts of their actions in a transparent way.
Is a material locally sourced? How far has it travelled to be manufactured? Can a product’s origins be traced? Is the environmental impact of the product reported for some or all of its life cycle?
Asking questions like these of a single product is one thing. But in a system like a building envelope specification, there are multiple products and many ancillary components. It’s highly unlikely that a single manufacturer will produce all of those products and accessories, meaning those questions then have to be asked of multiple manufacturers.
How does a system supplier demonstrate traceability?
A system supplier controls their production process and product performance, and can therefore use consistent material supply routes. They can also work with trusted partners - who can prove their own quality processes - to provide a complete solution, within which is a variety of options for the specifier to choose from.
This is the approach that Tata Steel takes in offering building envelope solutions and providing the Platinum® Plus guarantee of up to 25 years.
All of Tata Steel’s UK-manufactured construction products are certified to the BES 6001 responsible sourcing standard, and have been since 2014. BES 6001’s assessment criteria cover product manufacturing, the management of Tata Steel’s own facilities, and responsible sourcing from the mines where iron ore is first obtained.
Tata Steel also operates and maintains a fully integrated, local supply chain. Steel is transported between different manufacturing sites by existing rail links, with systems in place to demonstrate exactly what materials have been used, and where.
In terms of reporting life cycle information, Tata Steel has spent nearly two decades developing expertise in life cycle assessment (LCA). Product-specific, externally verified environmental product declarations (EPDs) are available for all products, and Tata Steel was the world’s first steel company to be approved as an EPD programme operator.
All of the products offered by Building Systems UK are affixed with the CE Mark (and will have the UKCA Mark before Jan 2023), and are tested and certified by third parties like LPCB and FM. In fact, these approvals are not just an accreditation to do with product testing, they are an audit trail through the complete production process.
Responsible sourcing certification, supply chain auditing, LCA and EPDs, and extensive product testing all help to demonstrate the performance and environmental impact of system solutions backed by the Platinum® Plus guarantee.
To find out more, view Tata Steel UK's Building Systems UK range of solutions, or contact the technical team.
Alternatively contact our technical team today below:
T: +44 (0) 1244 892136