Client: St Modwen
Main contractor: Magrock Ltd
Roofing contractor: Ridgeway Facades Ltd
Architect: Roberts Limbrick
Products: Trisobuild® roof and wall, Trimapanel® and Colorcoat HPS200 Ultra®
Year: 2023
Location: Avonmouth
St. Modwen Park Access 18 Avonmouth required more than 20,000 linear metres of Building Systems UK’s Trisobuild® site assembled, roof and wall systems at their new high-spec warehouse space. A range of smaller units from 5,924 - 25,169sq ft have been completed and are available for immediate occupation. Further units will be delivered during 2023, ranging from 43,000sq ft - 204,000sq ft.
For Units 23, 24 and 25 Building Systems UK products were installed across over 20,000 linear metres of the building envelope using the Trisobuild® System. The project also houses office areas and meeting rooms.


As part of Units 23, 24 and 25 development St Modwen’s required a solution that can cater for various requirements in order to help secure occupants of any sector that may wish to reside within. Some of the current local occupiers around the site include organisations such as Amazon, ASDA, Peugeot, Evri, Co-Op and many more.
With a wide array of varying needs it was important that the building envelope could accommodate for any of these particular organisation types and also provide a highly aesthetically pleasing exterior for the local area and appeal to potential suiters.
With St Modwen’s key goal being about ‘creating sustainable commercial developments to benefit all involved’ it was vital a building envelope solution was utilised. With real estate at a premium it was also imperative the system could be installed efficiently and quickly in order to get the units filled as soon as possible.
Building Systems UK (A Tata Steel Enterprise), worked with the supply chain and were able to offer them a wide range of responsibly sourced, sustainable roofing and walling products from one single source UK manufacturer. This enabled the creation of an optimum building envelope solution to meet structural, energy efficiency and air tightness requirements, as well as offering a wide choice of aesthetic colours and finishes to create the visual impact required.
Building Systems UK’s, Trisobuild® site assembled roofing and cladding system was chosen with over 12,000 linear metres used for the roof and nearly 8,000 linear metres to form the walls. The Trisobuild® system can be tailored to meet the specific requirements of a project by offering design flexibility of internal and external profiles ranging from 19mm to 46mm deep. For this project, R32 and C32 and CL19 profiles were chosen for most of the roof and wall profiles respectively, all with Colorcoat® prefinished steel available in a range of colours.
By utilising wall and roof products from Building Systems UK with Colorcoat® products, St Modwen were reassured with the supply of the 40-year Confidex® Guarantee covering the long-term performance of the finish. Trisobuild® with Colorcoat HPS200 Ultra® pre-finished steel was chosen. The HPS200 finish they opted for included an array of colours including Goosewing Grey, Albatross and Merlin Grey to give a clean and attractive look to the external areas of the project.


By utilising all the roof and cladding products through Building Systems UK, the supply chain could be confident that the walls and roof of the warehouse and logistic units would work together seamlessly to provide a robust external envelope.
Trisobuild® is also third party certified for quality, fire safety, acoustic and thermal performance, as well as air tightness and water penetration. In addition, due to Tata Steel’s commitment to sustainable practices, both products are also certified as ‘very good’ to the BRE’s standard BES 6001, allowing maximum credits to be obtained in the responsible sourcing of materials section in BREEAM.
Building Systems UK could also offer a wide range of flashing, ancillary items, integrated windows, and fabricated corners to add the finishing touches to the distribution centre to deliver the desired aesthetic design for the project.
The correct installation of all panels and ancillary products is vital and Building Systems UK supplied a raft of standard junction details as a step-by-step guide to ensure that all interfaces were correctly constructed. In this way the roof and wall panels could be joined correctly to form a building envelope for the units and provide low air permeability to help enhance its energy efficiency and lower its CO2 emissions.
For extra reassurance the St Modwen Access 18 Avonmouth warehouse and logistic centres are also covered by a Platinum Plus 25-year building system envelope guarantee. Building Systems UK created a bespoke Platinum® Plus specification that considered how the components used on the project influenced and interacted with each other and what impact that would have on building design and performance. The comprehensive guarantee included such items as panels, pre-finished steel, stainless steel, sealants, fillers and flashing and gutters and came with a list of recommended approved suppliers for the project – Magrock Ltd carried out the installation work to the highest of standards and assisted greatly to the smooth and efficient fixing within the required timescales. Building Systems UK’s technical experts visited the site during the construction of the building to ensure that the agreed specification was being followed.
Using proven products from Building Systems UK (A Tata Steel Enterprise), backed by their team of experienced construction professionals and associated contractors allowed for the smooth delivery of St Modwen’s latest units - 23, 24 and 25.

EN-Construction-Contact-BSUK envelope
Building Systems UK technical team - Building Envelope
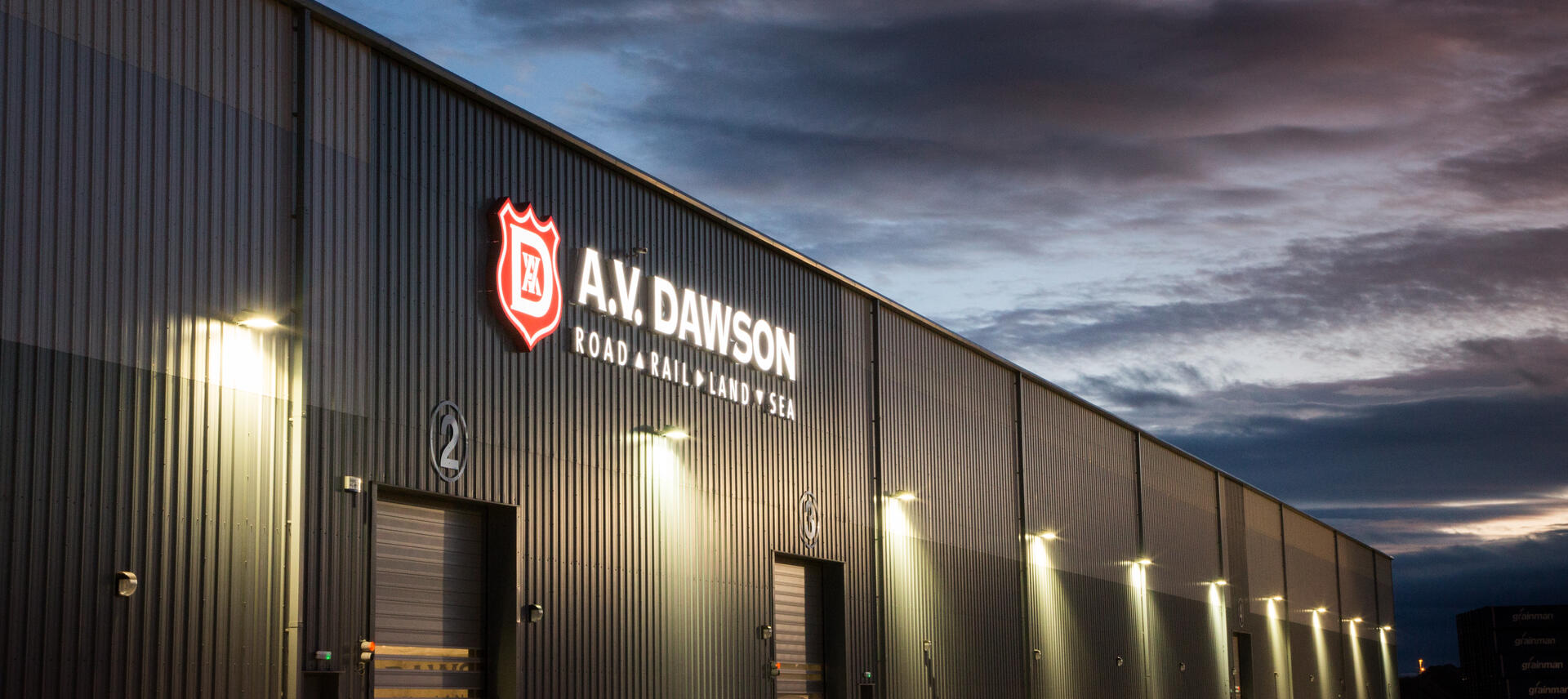