EN 10210 is the standard for hot finished hollow sections, and covers a number of subtly different products, manufactured in different ways and with different properties. Our Celsius® range is designated within the standard as S355NH because it is full-body normalised.
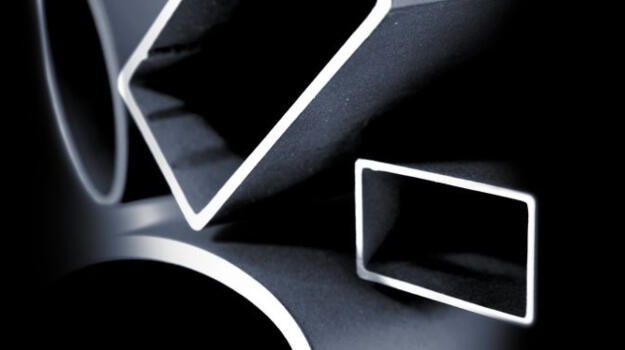
Our range of hot finished structural hollow sections is produced in accordance with the Euronorm standard EN 10210. There are many advantages to using EN 10210 structural hollow sections rather than a cold formed EN 10219 alternative, but even within the standard there are differences which aren’t always obvious, but could make a big difference to the end-user, the structural design engineer and the fabricator.
EN 10210 is the standard for hot finished hollow sections, and covers a number of subtly different products, manufactured in different ways and with different properties. Our range is designated within the standard as S355NH because it is full-body normalised. This means that the steel has been heat treated to at least 850°C and shaped while hot, rather than some products sold to the same standard which have used a lower temperature heat-treatment to relieve some stresses in a cold-formed product.
The three main manufacturing routes for steel tube sold to the EN 10210 standard are:
- Partially stress relieved
- Fully normalised
- Seamless
These routes can be seen in a diagrammatic way in the figure below, which also shows how these relate to the simple cold-formed tube manufacturing route.
It is widely understood that when a cold formed hollow section is produced, stresses are put into the steel in the shaping and forming process. This differentially hardens the steel, particularly at the corners and along the weld-line, which reduces ductility and produces points of weakness in the structure along which cracks could form (Figure 1).
Heat-treating the steel can relieve these stresses somewhat but, for the reasons explained below, the temperature of this heat treatment is important in determining how many of these internal stresses are eliminated.
The easiest way to explain the effect of heat treatment is by using the carbon steel phase diagram (Figure 2). This shows that the internal microstructure of the steel is affected by temperature.
When steel is heated into the austenitic phase this is called normalizing. During the normalizing treatment a new fine grain structure of austenite is formed and as a result internal stresses created during the formation of the tube are eliminated. Heating the steel to lower temperatures does not enable growth of new austenitic grains and although the heat treatment allows some internal stresses to be removed it will not eliminate all of them.
Internal stresses can be points of weakness along which the tube could crack, so elimination of these stresses is essential for reducing the possibility of in-use failure. The uniform structure achieved by normalizing also means that any further processing, such as welding, will be predictable – there will be no ‘hard’ spots that will behave differently on welding.
Typically, structural hollow sections have a carbon content around 0.2% and looking at the diagram, only at temperatures above 850°C will the steel enter the austenite phase. That’s why we always do the final forming of our Celsius® sections at normalizing temperatures, to give the best, full-body normalized properties.
Hollow sections which are stress-relieved at lower temperatures are not fully normalized, so some residual stresses will remain, particularly around the weld. Importantly, the EN 10210 standard allows this, so it is vital to understand the difference. A good demonstration of the difference between a cold-formed, stress-relieved and fully normalized hollow section can be seen by examining the hardness on a cross-section of a sample of each type.
Harder steel contains more stresses and so is more prone to failure, while variations in ductility can produce weak-spots in a structural section. The images below show a visual representation of just such a demonstration, investigating hollow sections with the same tensile strength but produced in different ways. The colours on the images represent the results of micro-hardness tests on three sections, all with a specific minimum yield strength of 355 N/mm2.
The images at the top show a fairly uniform hardness across the flat edge of a cold formed hollow section, but the weld and the corner show where greater stresses have been imparted, leaving harder, less ductile steel.
The images in the middle show that stress-relieving does improve the ductility of the bulk of the hollow section, but around the weld and the corner, areas of high hardness remain. The real-life behaviour of this stress-relieved hollow section will not be much better than the cold formed one, since failure would be initiated at the areas of low ductility (the dark areas on the diagram).
Finally, the fully normalized hollow section at the bottom shows a uniform and low hardness throughout, giving the highest ductility and best failure-resistance.
With both the stress-relieved and fully normalized hollow sections complying to EN 10210, it could be difficult to know what you are getting. But here the standard actually helps. Within the EN 10210 standard, a hollow section designated as S355NH must be fully normalized, whereas one designated as S355J2H can also be stress relieved. So by specifying S355NH (the ‘N’ stands for normalized!) you can be sure of getting the full benefits of a true hot finished hollow section.
A fully normalized hollow section is better to process due to the lack of residual stresses and has outstanding dimensional stability during a long service life. In addition, because the final shape is formed at the normalizing temperature, fully normalized square and rectangular hollow sections can have much tighter corner profiles without any deterioration of properties at the corner. Our range of structural hollow sections, which are fully normalized, have a corner radius which is always less than 2T, whereas stress-relieved sections often have much slacker corners, up to 3T in radius. Apart from the obvious aesthetic benefits of tighter corners, they also present a larger and more uniform flat surface for welding.
So, in summary, there are many benefits to a true hot finished hollow section and specifiers need to be wary of products which may be compliant to the standard, but which don’t provide the full risk reducing benefits. By specifying a fully normalized hollow section, using the designation S355NH, you can always be sure of achieving the best performance in use.