2018 was a significant year for us, marking the 20th anniversary of our specially formulated Galvalloy® metallic coating and also the unique Scintilla® emboss, both of which were introduced in 1998.
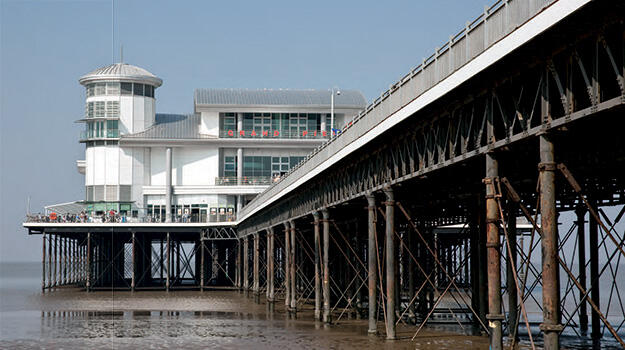
2018 was a significant year for us, marking the 20th anniversary of our specially formulated Galvalloy® metallic coating and also the unique Scintilla® emboss, both of which were introduced in 1998.
Prior to this date, the industry standard for manufacturing pre-finished steel products involved applying a zinc metallic coating, often referred to as Hot-Dipped Galvanised steel. The science behind the concept was that the molten zinc would coat the steel, providing a robust defensive layer and protecting the steel beneath from corrosion, ensuring it would last longer than uncoated steel.
While this process provides improved levels of durability and endurance, it does still have limits. For example, this solution is not always robust enough to perform in particularly aggressive environments, consequently leaving the steel vulnerable to corrosion. Therefore in 1998 we revolutionised the industry by introducing our own metallic coating for the galvanising process – Galvalloy®.
A carefully developed mix of 95% zinc and 5% aluminium, the Galvalloy® metallic coating is designed to improve the corrosion resistance of a pre-finished steel product by slowing the breakdown rate of the metallic coating and offering a combination of increased barrier and sacrificial protection, when compared with the conventional 100% zinc metallic coating.
This has further benefits when it comes to the longevity of the top coat as the layers adhere to the eutectic structure, reducing the risk of edge peel to the final product.
To coincide with the introduction of Galvalloy®, we also introduced the Scintilla® emboss, ensuring that our product (originally named Colorcoat HP200®) and the unique Galvalloy® metallic coating was clearly identified as such.
Branding products with an emboss was not entirely a new idea, with many manufacturers already using a leather grain emboss on their products at this time. However, this emboss did not carry any exclusivity or distinction to a brand or product, being both simple to produce and fairly commonplace within the industry.
In addition to this, the leather grain emboss was potentially more damaging to the pre-finished steel, with the substantial depth of the emboss encouraging dirt to become trapped and making the maintenance and cleaning of the structure more difficult.
It was because of this that the Scintilla® emboss was such a revolution, being both a unique identifier and mark of authentication for the brand and also Shotton Steelworks, where the pre-finished steel was, and still is, manufactured. The Scintilla® emboss is shallower, only a nominal 50 microns in depth, meaning that it is less likely to trap dirt than the leather grain alternative, therefore enhancing the protection against corrosion.
The subtle design clearly identifies the steel as being a superior product. While the emboss is noticeable on close inspection it is not visible from a distance, meaning that the visual aesthetic of the overall structure is not affected.
At Tata Steel, we are always looking at ways to develop our range of pre-finished steel products further, improving their resilience, protection and colour preservation. By further developing the manufacturing process over the last twenty years, the innovative Galvalloy® metallic coating is now just one of several layers that serve to protect the steel underneath, all working together to produce the superior and exceptionally durable pre-finished steel product available today.
To find out more about our range, we offer a CPD which takes the visitor on a tour of the Shotton Works site in Deeside. The guided tour encompasses all aspects of the production process and is completed by a technical presentation, providing additional detail about the manufacture, testing specification and utilisation of the products. The total duration of the visit is half a day.